Schimmelbusch Irrigation Syringe
Even minimal changes in temperature and humidity endanger preservation of museum objects. Objects are composed of different materials, which react differently to climatic changes. Schimmelbusch irrigation syringe, made of metal to allow heat sterilization, can serve as an example. Since the early 20 century, instrument makers delivered syringes upon request in simple wooden cases.
Decrease in humidity and temperature shrinks the wood of the case, while the nickel alloy of the syringe itself retains its volume. Suddenly, there is not enough space for the instrument. In our case, the front side of the case gave in under the pressure of the syringe conus. The conservator mended the case, but had to find a long-term solution as well: the metal/ wood combination appeared to be sensitive to climatic changes and even with best care, the problem can return in the future. The original instrument makers themselves often carved or drilled small holes in the wood to make space for the conus, viz. handle of the instrument. The conservator chose this method as well: the syringe with its conus fits the designated space well, but without undue pressure. The object will easily resist moderate changes in humidity and temperature in the future.
Similar reasons inspired the invention of the Schimmelbusch syringe. The name of German physician Curt Schimmelbusch (1860-1895) is most commonly linked to the ether and chloroform narcosis mask he introduced in 1890, one commonly used until the 1950s. Schimmelbusch was a prominent advocate of asepsis in medicine and surgery. He suggested improvement to the autoclave and introduced boxes, used till the present day, in which instruments and bandages were placed in the autoclave without being touched and thus contaminated. Aseptic considerations motivated him in devising both the mask and the syringe as well.
Schimmelbusch recommended an all-metal syringe in the 1890s, shortly before his premature death of tuberculosis. He appears to have never explicitly claimed the design: he may have participated in devising the syringe or introduced it to clinical practice. In the second edition of his famous Anleitung zur aseptischen Wundbehandlung (Guide to the aseptic treatment of wounds, 1893) he described a practically identical syringe under the name of the manufacturer, Christian Schmidt. (Schmidt’s company was located in Ziegelstrasse, next to Berlin surgical clinic where Schimmelbusch worked.) In the Guide, Schimmelbusch drew attention to cases of neglecting asepsis in hypodermic injecting. Whether the contagion was transferred by the injected liquid, the needle or the syringe and its piston, patients were infected with anthrax (Breslau), tuberculosis (Vienna) and other diseases when syringes were not sterilized between uses. According to Paul Ehrlich’s report, two patients injected by the same syringe died of edema at the Berlin Charité hospital in 1882.
The issue fatal to our syringe case complicated, however, effective sterilization of syringes with boiling water or hot air. Diverse materials – metal, glass, asbestos or linoleum in the piston – reacted differently to heat and the glass body of the syringe cracked. The Schmidt all-metal syringe offered a solution. “From our own experience we are assured that this syringe conforms to all requirements of an aseptic instrument, with the single objection of being non-translucent. The cylinder is composed of nickeline, and the piston bulb is made from a thin, elastic, concave piece of nickel which fits closely to the walls of the barrel. The free passage of the surfaces over one another is facilitated by a light smearing with Sarg’s glycerine. Oil is avoided. The syringe is always ready for use, and is not damaged by boiling.”
Explicit references to the „Schimmelbusch syringe“ appeared in the late 1890s: the German medical expedition that set forth to study plague in Bombay in 1897 was equipped with two 100 ml „Schimmelbusch aseptic syringes“ with metal pistons. The eponym became quite common in early 20 century catalogues, especially in German-speaking area. The syringes were produced in various sizes both for injection and irrigation. The larger irrigation version was equipped with two metal cannulas: a conic one for wound irrigation and urine extraction and an olive one for irrigating the intestine (enema) and other organs. Schimmelbusch recommended sterilizing the cannulas by boiling in water or better, in sodium hydroxide. Cannulas made of platinum and iridium alloy, rather than steel, could be disinfected by direct fire. The cannula and the body of the syringe were in any case sterilized apart and the difference in expandability could be neglected.
Schimmelbusch himself mentions opacity as the main disadvantage of metal syringes: the physician can see neither the nature of the injected liquid, nor the impurities it may contain. Medical practitioners came to prefer, especially for injections, all-glass syringes (Jeanne Amélie Lüer, 1896) and modular syringes of glass and metal (Rekordspritze, Dewitt & Herz, 1906). Compared to glass, metal syringes were practically unbreakable, but with the falling prices of the instruments, this became less of a concern.
Thanks are due, above all, to Mr. Frantisek Nič, restorer and conservator, Krkonoše National Park, Krkonoše Museum Vrchlabí.
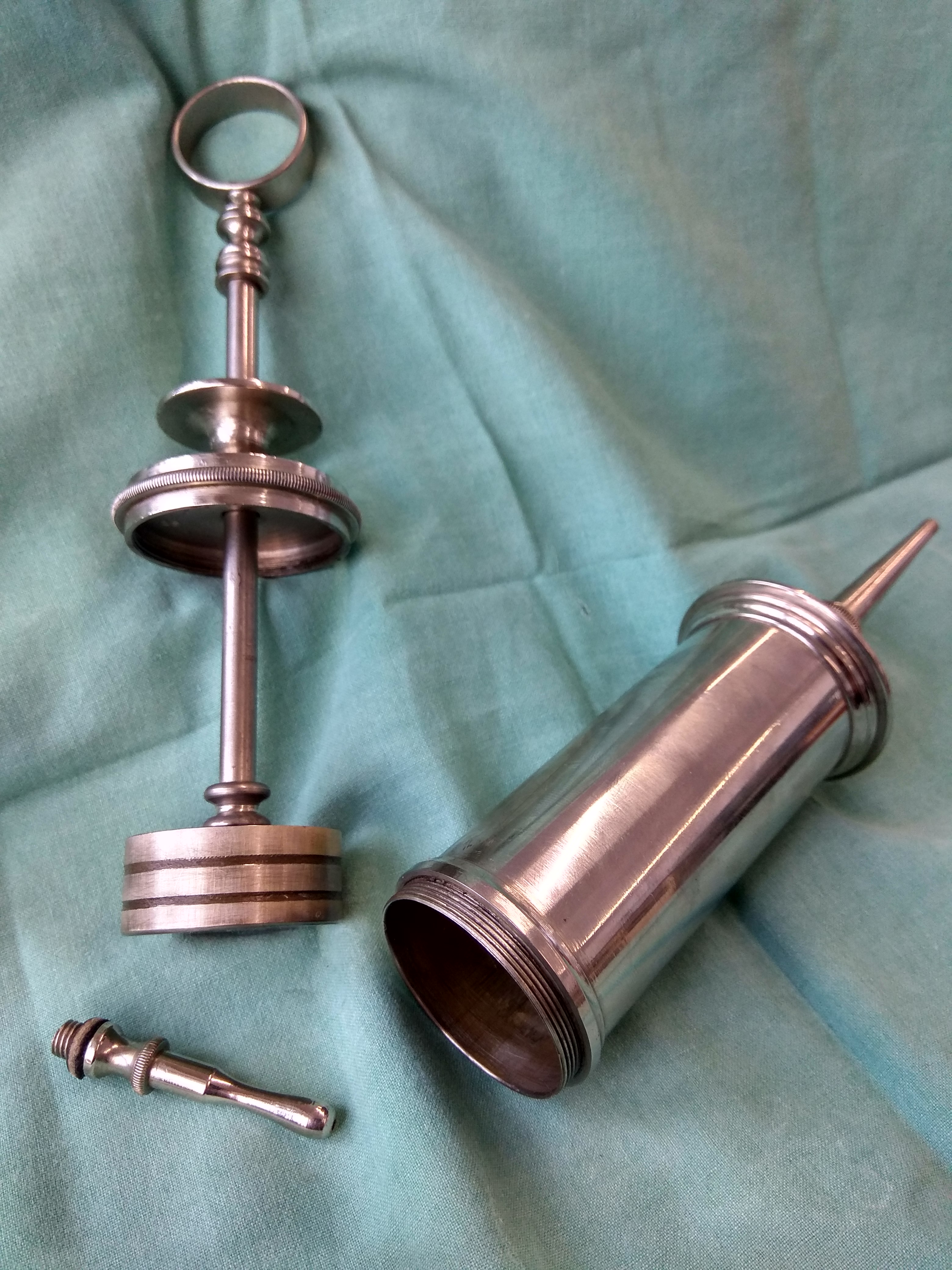
Photograph by Petra Lendlerová